Lufthansa Technik Philippines is a global provider of maintenance, repair and overhaul services for commercial aircrafts. With the location of a 4-hour flight radius to Singapore and Hong Kong, this strategic facility in the Asia Pacific rim provides strategic servicing to customers worldwide.
- Lean Six Sigma
QuickAdopt approach of training, application and coaching laid a foundation in sustained culture of continuous improvement
$3.1M per year savings achieved within 3 months of the 2-year plan
The Client
The Challenge
Faced with mounting pressure from global competitors, the Lean program management team needed a Lean implementation and training program customized to enable the Philippine workforce to increase their productivity and secure more business.
Following the introduction of a new aircraft type, the Lean management team also needed to improve efficiency and increase capacity to maintain its competitive advantage within a 2-year target. As the shop mechanics prepared for servicing a new aircraft type, the Lean management team wanted to reduce cycle time for the current process by 15%.
Our Methods
Kairos Worldwide began with an assessment of a pilot division and the establishment of QuickAdop, a Kairos Lean Six Sigma program. Included were customized training, Lean project application, and coaching team members to navigate through the project life cycle. To introduce QuickAdopt most effectively, multiple Lean teams were created. The goal was to facilitate Lean analysis, applying tools that would build organizational capability within short time frames.
After reviewing process flows and interviewing internal stakeholders, Kairos Worldwide led the Lean teams in their work on the floor. Along with management, we prioritized ROI opportunities having the greatest potential for significant impact. This QuickAdopt approach improved cycle time, labor productivity and customer satisfaction within three months, well ahead of the client’s two-year target.
The Impact
Cycle Time
- 26% aircraft turnaround improvement compared to 15% target, increasing customer satisfaction by releasing aircrafts to customers sooner
- $120,000/year savings realized for purchase, delivery and use of tools
Labor Productivity
- 23% labor savings achieved by a reduction in labor hours
- Reduction in the need for overtime achieved by redesign of tool setup procedures
Sustainability
The QuickAdopt approach of training, application and coaching laid a foundation in sustained culture of continuous improvement. Other teams immediately “raised their hands” for implementing Lean tools in their shops. A digital dashboard displayed progress and bottom-line impact. Three years after the Lean implementation, the departments had been using Lean Six Sigma principles and implementing other projects. Kairos Worldwide was invited back to act as a judge for a Lean Competition.
QuickAdopt promoted the effectiveness of the Lean concepts across the company. Quick adopt. Quick change. Quick Wins.
SHARE THIS ARTICLE:
Let’s Work Together
Need help with transformation, or have a question about change management? We’re here to help.
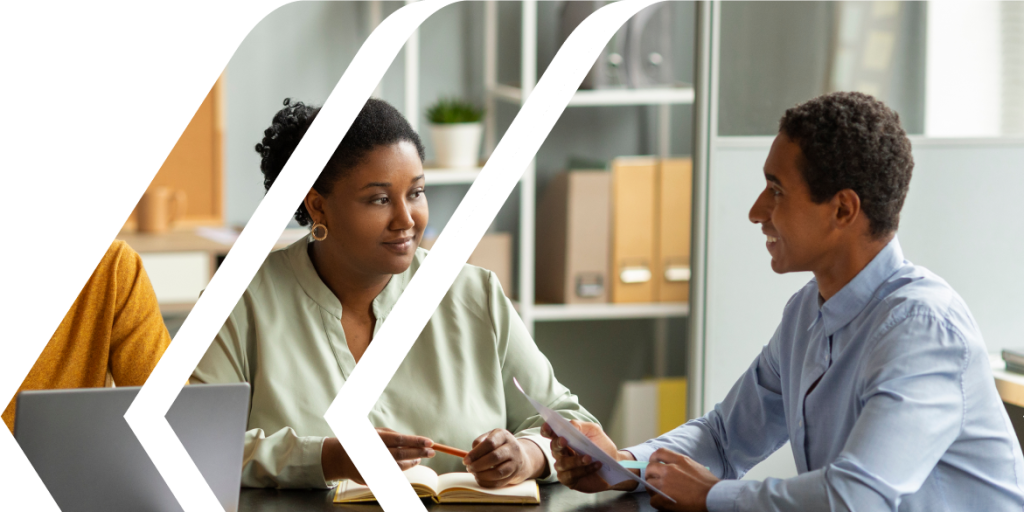
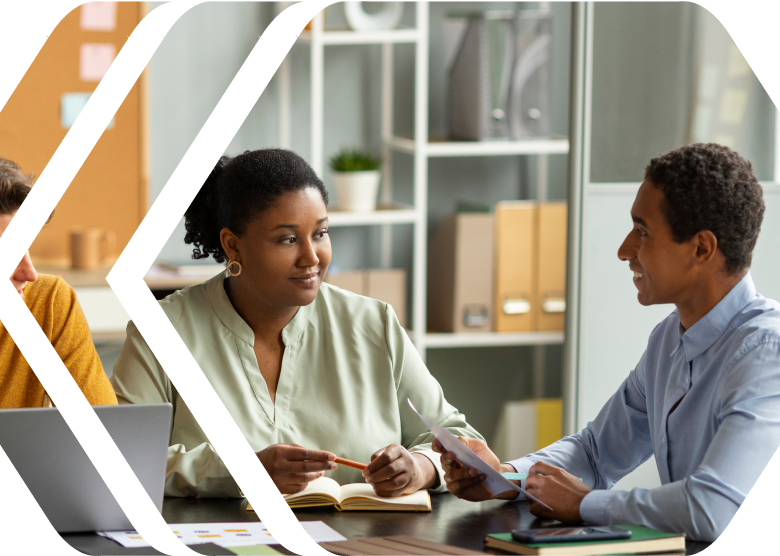
Let’s Work Together
Need help with transformation, or have a question about change management? We’re here to help.